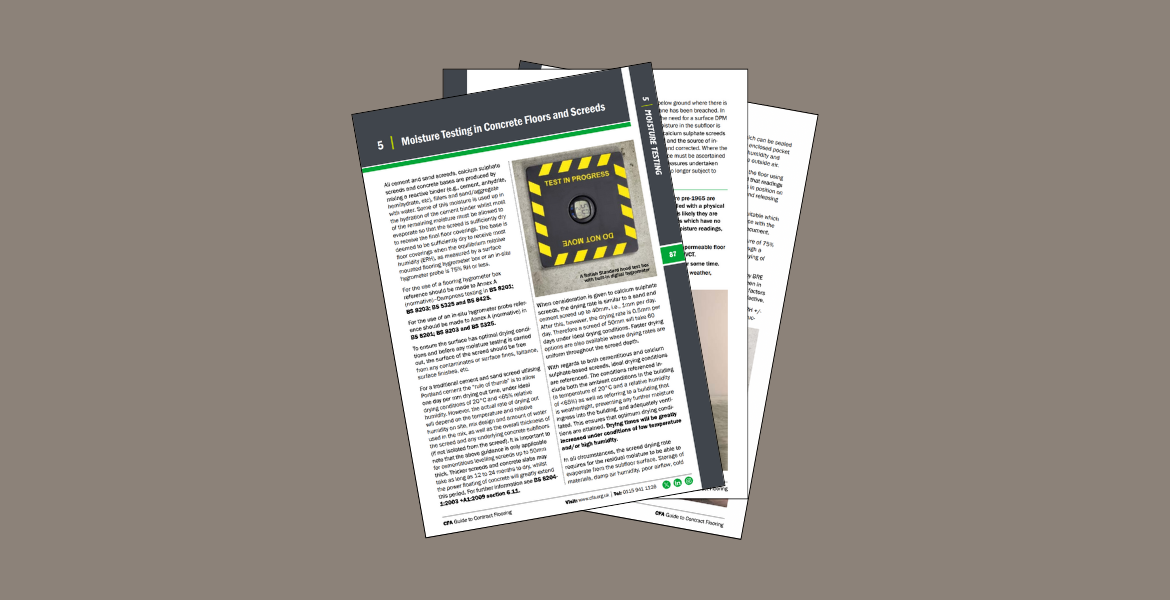
In order to achieve a problem-free installation, it is essential to ensure that the slab and screed are adequately dry before laying floor coverings. That is, when the equilibrium relative humidity (ERH) is 75% or less when appropriately and correctly measured.
BS 5325, BS 8201 and BS 8203 all reference the hygrometer box method as being the correct test for measuring the moisture content of floors prior to laying floor coverings; however, there are other methods available which can either be used instead of or as support in some circumstances. These include the hygrometer sleeve (also known as the in-situ method), radio frequency (RF) detectors, electrical impedance meters, pin meters, carbide bomb (CM) testing and gravimetric oven testing.
Hygrometers measure the relative humidity of an air pocket in equilibrium with the floor. They are the definitive method for assessing the moisture content of subfloors and are recognised in British Standards.
The hygrometer box is a non-destructive method for measuring the moisture content of slabs and screeds and is the most commonly approved method. Full details of the instrument and operation methods are given in BS 5325, BS 8203, BS 8201 and BS 8425.
The insulated permeable hygrometer box works by measuring an enclosed pocket of air which is isolated from the humidity and fluctuations of the outside air. This is done by sealing the box onto a clean and prepared area of the floor surface using a preformed butyl sealant tape, ensuring that underfloor heating and any other drying aids are switched off 96 hours before testing commences.
It is recommended that the test is performed on an area of screed deemed to be the wettest – generally in the corners of a room, out of direct sunlight or in an area which has poor ventilation. This can be determined by firstly checking the floor with an electrical impedance moisture meter.
The box should remain in position until full equilibrium is established, which is generally around 72 hours but could be longer over sections of 200 metres. This would take considerably longer when testing power floated concrete.
When measuring unbonded screeds where a damp proof membrane is placed between the base and screed, a period of at least 4 hours should be allowed before the first reading is taken.
Equilibrium may be assumed when two consecutive readings taken at 4 hour intervals show no change, the hygrometer may then be removed.
A floor is deemed to be sufficiently dry to receive most floor covering when the reading is not greater than 75%, although when laying some timber finishes on underfloor heating the relative humidity should be not greater than 65% in line with manufacturers recommendations.
The hygrometer sleeve is another recognised method, for measuring moisture in slabs and screeds, introduced to the UK in 2011 with the revision of BS 8201. It was also included in the 2017 revision of BS 8203 and the 2021 revision of BS 5325.
Testing is performed by inserting a relative humidity probe directly into the slab/screed and allowing the sensor to equilibrate with a small pocket of trapped air to achieve an equilibrium RH reading. Because the airspace is situated inside the slab and can act as a better insulator against temperature change, the results are generally more stable than those given by the hygrometer box, however it is a destructive test and is therefore not suitable for use in screeds where underfloor heating pipes have been installed without knowledge of the exact location of the pipes.
To ensure that heat generated by drilling the hole does not affect the readings, British Standards recommend that the hole must be allowed to cool for a period of at least 72 hours with the proprietary sleeve in place before the probe is inserted. Additionally, readings can drift if the probes are exposed to humidity levels in excess of 93% for more than 24 hours. The probes can be removed as soon as a reading exceeds the required reading such as 75% or as recommended by the product manufacturer and further drying or the application of a surface DPM will be required.
RF detectors and impedance meters provide a quick assessment of the relative moisture condition from the surface of the slab/screed to a nominal depth. This does mean that the accuracy of the readings can be affected by on-site conditions such as high condensation within the building which can result in condensation forming on the floor surface, and the use of dehumidifiers which can give artificially low readings if not shut down at least 48 hours before testing is performed. To improve the accuracy of readings on flowing cementitious and calcium sulphate screeds, the surface of the screed should be fully sanded/abraded prior to the commencement of moisture testing.
Impedance meters provide an indication of the actual moisture percentage in concrete or screeds whereas RF detectors only show if the floor is “dry”, “wet” or “at risk”. There are many devices available which provide instant non-destructive readings from the concrete/screed surface and should be used as the best method to identify the most suitable area to locate a hygrometer box or sleeve.
PIN meters provide quick and accurate surface or subsurface moisture measurement at precise points. They provide actual moisture content percentage value in wood and wood moisture equivalent (WME) value in other materials. They measure the moisture content of a material by measuring the electrical resistance between two pins inserted into the material. The meter produces a reading that indicates the moisture content, which can be compared to a calibrated scale.
The carbide bomb method, which is a national standard in many European states, and the gravimetric oven dried sample test are acceptable methods of measuring moisture in slabs and screeds in accordance with the screeding standard BS 8204-7. Both are destructive tests involving removing samples from the screed or slab and are generally used by screed installers or manufacturers or when performing diagnostic testing.
When using the carbide bomb method, the sample removed from the screed is crushed in a mortar and pestle. The required amount is placed into an airtight container chamber together with calcium carbide which produces acetylene gas when it comes into contact with moisture. The result is instantaneous and read as pressure on the gauge, however, there is high potential for user error in addition to the test being destructive.
The carbide bomb method will not measure chemically bound moisture within a sample as calcium carbide reacts with only free-moisture. It is, however, ideal for testing the moisture content of some fast-drying screeds which act by chemically binding the majority of construction moisture and cannot be tested with relative humidity or electrical impedance devices.
Gravimetric oven testing requires the sample to be removed from the floor without too much moisture being lost. Testing is generally performed in a laboratory where the sample is weighed before and after being dried in an oven to calculate the moisture content by weight. There is a high potential for contamination of the screed sample and this test method is seldom used.
For more information on moisture testing, including how to operate hygrometers and complete other suitable tests, refer to the CFA Guide to Contract Flooring chapter ‘Moisture Testing’. For more specific references to acceptable equilibrium relative humidity (ERH) limits and other key updated guidance, the CFA has recently published a member-only guidance note on moisture measurement for in-situ probe method, accessible in the General Guidance section of the CFA’s Member Area.