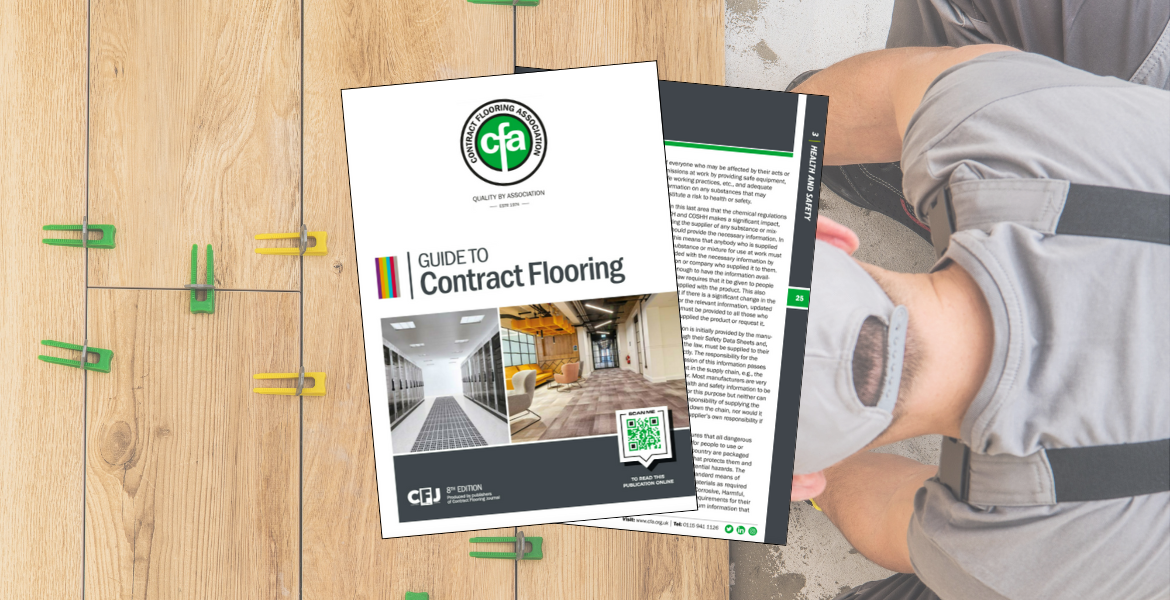
Details of hazard information relating to specific materials are supplied by the manufacturer in the form of safety data sheets (SDS) and should be passed on down the line of supply. Under existing Health and Safety legislation, it is the responsibility of the supplier to ensure that there is adequate information made available to enable the user to apply the material safely. Equally, the user also has responsibilities including asking the supplier, when necessary, for specific information. This is of particular importance when novel or out-of-the-ordinary applications are involved.
As a generalisation, read the manufacturers’ instructions thoroughly before any product is used.
Storage
Products will be labelled in accordance with the current UK or EU legislation. Some products will be labelled as “Highly Flammable/Flammable” and these must be stored in accordance with UK legislation and guidance.
Hygiene
Spillage
Any accidental spillages must be contained immediately by barriers of earth or sand (not sawdust). The spillage must be soaked up and disposed of in accordance with both local and national regulations. See SDS for more detailed information.
Waste Disposal
The Environmental Protection Act, the Waste Management Licensing Regulations and legislation arising from these Acts, relate particularly to: Duty of Care, Controlled Waste, Licensing Requirements and Special Wastes.
These require waste materials to be classified, separated by type, contained, stored, handled, transported, treated, and disposed of according to strict requirements by licensed agents, carriers, and treatment operatives. Supportive confirmatory documentation relating to proper disposal of waste should be kept as proof of “duty of care”. Additional checks on procedures and methods employed are recommended including proof of the receiver of the waste being legitimate.
Always refer to section 13 of the supplier’s health and safety data sheet for disposal recommendations of hazardous materials and their containers.
Vapours From Solvents
The vapours from solvent-borne products are generally harmful when inhaled, which may lead to nausea, headaches, dizziness, and unconsciousness in the short term and, in some cases, may lead to more serious long-term effects. A risk assessment should be conducted to determine the most appropriate method in order to reduce the exposure to vapours. This may include but is not limited to such actions as ensuring windows and doors are open and a through-draught is blowing.
If this condition cannot be achieved, use either a flameproof extractor fan (for factory applications) or an approved respirator, such as a fresh air fed mask fed with clean air or a suitable organic vapour mask as specified by the SDS.
Water-Based Products
Most water-based products have a low degree of hazard but in some cases small amounts of solvent will be present and the above precautions must be taken if so labelled. Take the precautions given in the SDS and use good practice.
Hot-Melt Adhesives
The major hazards associated with the use of hot melt products are burns either from molten adhesive or the applicator tip, or if a melt comes into contact with water when it will spit violently.
If burns do occur, immerse the affected area in clean cold water immediately. Do not attempt to remove the cold adhesive from the skin. Cover the affected area with a wet compress and obtain medical advice immediately.
Resin-Based Products
Liquid products such as epoxy resin, polishes, seals, lacquers, polyurethane, surface membranes and formaldehyde condensation products present no particular fire or explosion hazards unless they contain highly flammable or flammable solvents, in which case containers will be so marked. Under such circumstances, the precautions outlined for solvents should be observed. Take the precautions given in the SDS and use good practice.
Ensure adequate ventilation. Some components may be hazardous, and precautions will be stated on the label. Where components are powders, it is obligatory to use dust masks. Strict attention must be paid to the manufacturers’ instructions.
Dust
Dust from products, such as cement and from floor preparation operations such as sanding wooden floors, is a potential irritant and exposure to such risk should be controlled by care in handling, the wearing of personal protective equipment such as dust masks or respirators, eye protectors, gloves, etc., and the use of barrier creams. See www.hse.gov.uk.
Hardwood dust can cause cancer; both hardwood and softwood dusts have a Workplace Exposure Limit (WEL) which must not be exceeded. For further details and advice go to: www.hse.gov.uk/woodworking/wooddust.htm.
Spontaneous ignition can occur with sanding dust, collection bags and oily rags. These should not be left unattended even for a short time and must be disposed of safely.
Further information on health and safety can be found in the CFA Guide to Contract Flooring.