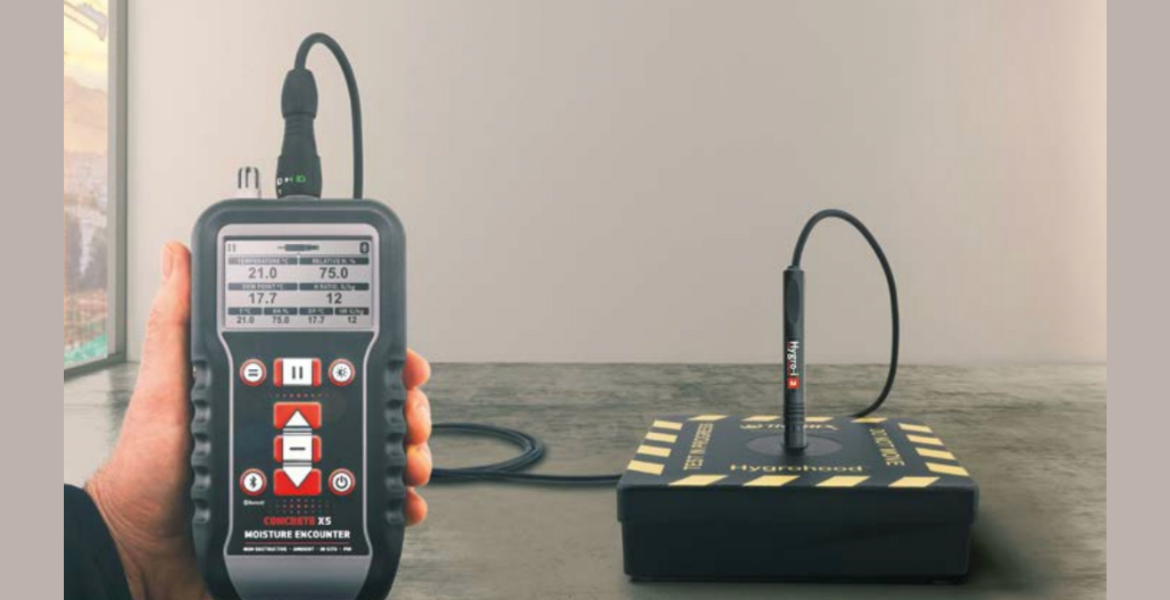
To prevent the adverse effects of high floor moisture, it is the duty of the installer to accurately test and control the equilibrium relative humidity (ERH) levels of a screed or concrete based floor. Responsibly low moisture levels are crucial to promote long-term flooring performance, creating a more lasting and therefore more sustainable installation.
There are two main categories of moisture that can lead to serious issues if not managed: construction moisture and building moisture. Construction moisture is associated with a newly built or in construction property, originating from sources like wet trades, rainwater ingress or high humidity levels. Building moisture refers to refers to persistent high indoor humidity in an already completed building, such as from insufficient ventilation, plumbing leaks, or even everyday activities of occupants such as cooking and showering. In both cases high moisture levels can introduce harmful substances like soluble salts and other minerals, resulting in complications such as efflorescence, delamination, and mould growth.
The recommended test for ERH is performed through a hygrometer, either a hygrometer box or an in-situ hygrometer probe. To ensure the surface has optimal drying conditions and before any moisture testing is carried out, the surface of the screed or concrete base should be free from any contaminates. For a traditional cement and sand screed utilising Portland cement the ‘rule of thumb’ is to allow one day per mm drying out time, under ideal drying conditions of 20°C and <65% relative humidity. However, there are a number of factors that will impact the drying time, such as the type of screed used or environmental factors. Thicker screeds and concrete slavs may take as long as 12 to 14 months to dry, whilst the power floating of concrete will greatly extend this period. Furthermore, drying times will be greatly increased under conditions of low temperature and/or high humidity. Force drying with the aid of UFH or dehumidifiers when responsibly used can help reduce drying times significantly.
If ERH is too high, there is a need to introduce a surface DPM to control the excess moisture in the subfloor. Floor slabs which are pre-1965 are likely to not have a physical DPM or, if they were, then it is likely they are no longer effective. However, in the case of calcium sulphate screeds the use of a surface DPM is not recommended and the source of ingress must be identified and corrected. Floor slabs which have no effective DPM can still give low moisture readings if they have been installed with a permeable floor covering such as carpet or VCT, have been left uncovered for some time, or are tested in a period of fine weather, where groundwater is low. If any doubt exists a surface DPM should be applied to avoid potential problems.
Whilst BS 5325, BS 8201 and BS 8203 references the hygrometer box method as the correct test, there are other tests available which can provide support in the right circumstances, such as the Carbide Bomb (CM) test and the Gravimetric dried sample test, both of which are acceptable under the screeding Standard BS 8204:7.
For more information on moisture testing, including how to operate hygrometers and complete other suitable tests, refer to the CFA Guide to Contract Flooring chapter ‘Moisture Testing’. For more specific references to acceptable ERH limits and other key updated guidance, the CFA has recently published a member-only guidance note on moisture measurement for in-situ probe method, accessible in the General Guidance section of the CFA Member Area.