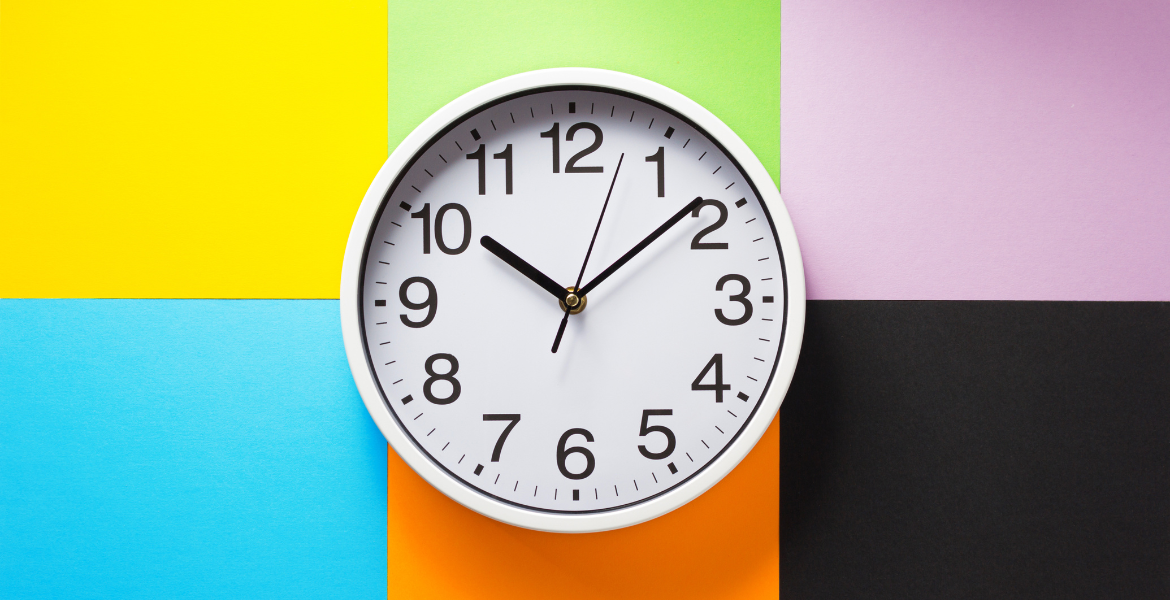
Understanding the importance of drying times for screeds is crucial for anyone involved in construction or renovation projects. One of the main reasons for floorcovering installation failure is excess subfloor moisture. It is essential that all those involved in the installation understand that application of the surface finishes before drying out has been completed may lead to failure unless suitable moisture mitigation/surface DPM systems are utilised.
Sufficient time should be allowed in the build programme to allow the subfloor to properly dry prior to the application of floorcoverings. The amount of time required can vary greatly based on screed tpye as well as in response to a number of external factors including not only the amount of water used in the mix design but also the site conditions at the time of laying, the post installation site conditions and the depth of the material. Where sufficient time cannot be allocated moisture management systems such as liquid DPMs and over lay systems can be considered in order to mitigate the risk that remaining moisture does not affect the final performance of the finished floor coverings. It should be borne in mind that the laying of concrete externally where it directly affected by atmospheric conditions is common practice in the UK.
Drying times will vary according to the product used and manufacturer’s guidance should always be sought on the appropriate drying times. Drying times are usually based on 40 to 50mm depth in warm and well-ventilated drying conditions, typically <65%RH at 20°C. Poor site condition and deeper screed sections will extend drying times so it is very important to ensure site conditions are well controlled.
The general recommended drying times for traditional sand and cement screeds of up to 50mm thickness is one day for every one millimetre of screed. It should be noted that thicker screeds may take up to 12 to 24 months to dry and for concrete with a power floated finish the drying time will be greatly extended. Reference should be made to BS BS 8204-1:2003 +A1:2009 section 2.11 for further information.
Calcium sulphate screeds up to 40mm thick should be allowed to dry for one day per millimetre. This then increases to two days per millimetre thickness for every millimetre of screed above 40mm, meaning that a 50mm thick screed will require a minimum of 60 days drying time. In this example, the drying time accounts for 40 days for 40mm thickness plus 20 days for the additional 10mm.
With all screeds, drying rates will be impacted if the evaporation of moisture from the screed or concrete is impeded by factors such as low on-site temperatures, high humidity, poor airflow, water spillages from other trades and water ingress into the building.
Good ventilation or the use of dehumidifiers can assist in reducing the ambient humidity. Forced drying of these screeds is possible if required. After 3 days dehumidifiers maybe employed, and after 7 days the UFH may be commissioned and slowly brought up to temperature to force dry the screed, reducing drying times significantly.
To ensure the smooth installation of floor screeds and subsequent floorcoverings it is advisable that all parties have a clear understanding of the requirements and programming required. To ensure that this is achieved it is suggested that all parties involved in the project consult at an early stage in the contract.
Application of primer promotes good adhesion of smoothing underlayments and prevents premature drying.
For more information on drying, refer to the CFA Guide to Contract Flooring chapter ‘Substrates’.